汽车车灯反光条及反射镜结构设计要点
Lamp mold are mainly used for lighting parts , which can be said to be the eyes of the car. Car lights are a general term for all automotive lighting systems. The appearance requirements of automobile lights are high, and several important parts are transparent parts, electroplated parts, etc. It can be said that the parts with the highest appearance requirements of automobiles are lights, so the requirements for mold design and manufacturing are extremely high.
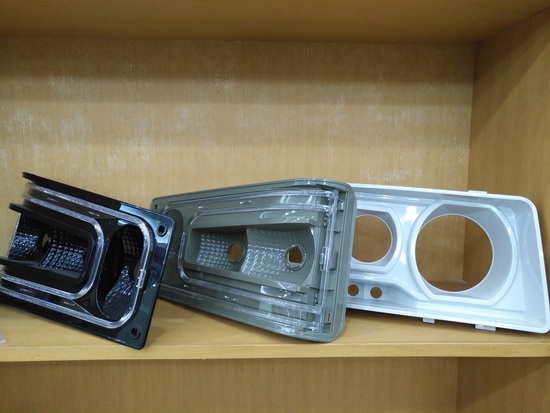
Gate location method: Do mold flow analysis, and confirm the cavities and position of gate points and weld lines to customers. Before cutting the mold, the position of the welding line needs to be confirmed by the customer. Mold steel material: NAK80 or S136H is used for transparent products, original material proof is required, and the hardness of the cavity and core block molds is staggered.
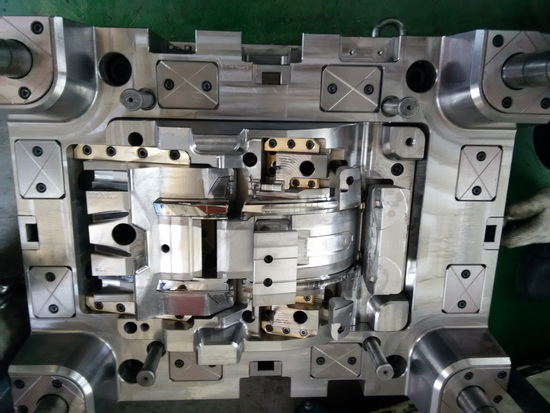
The cavity mold of the reflective product adopts NAK80 or S136H (HRC32-36), and the original material certificate is required. The rear mold can use forged steel HRC30-34. BMC material products are made of 8407 steel for front and rear molds (to achieve mirror polishing effect-A0 level ), and the original material certificate is provided, the hardness of cavity mold is HRC46-50, and the core mold is HRC44-48.
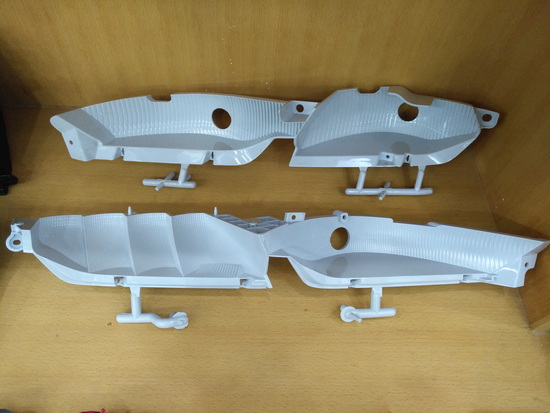
The steel of its products is forged steel (to achieve polishing effect) HRC32-36, the side of the inner core-pulling part is 0.03MM empty, and wear-resistant blocks are added. The exhaust is opened to the outside of the mold base, the exhaust is opened to the front mold, and the PL surfaces of the front and rear molds are effectively sealed to avoid air. Increase the area balance block and need to open the exhaust slot.
Transparent products/astigmatism products are polished, do not pass whetstone, save the mold to 1000# sandpaper and then polish, other parts are ordinary 600#, BMC mold/glue surface/pattern surface: CNC do the medium light and then discharge the mold, and then after the mold is completed The high-speed machine is in place at one time, 20,000 revolutions, and all the glue position parts of the rear mold are assembled together. BMC molds are polished with a knife below 3MM. BMC product steel cannot be welded, and aluminum-plated steel cannot be welded.
If the transparent/patterned material needs to be welded, the steel material needs to be cut from the material, polished and then fired, and tempered. For products made of BMC material, there should be no sharp corners (including bottom holes) on the mold. Before hardening Deep hole drilling to process the heating tube hole (positive 0.02), with the heating tube added hard, the heating tube itself is negative 0.05-0.1.
The top block of the perimeter needs to be inclined at 2 degrees to prevent the product from being clamped. Avoid sharp corners, and the R angle should be as large as possible. Heat treatment process and quality (can be hardened in the material factory) vacuum heat treatment.
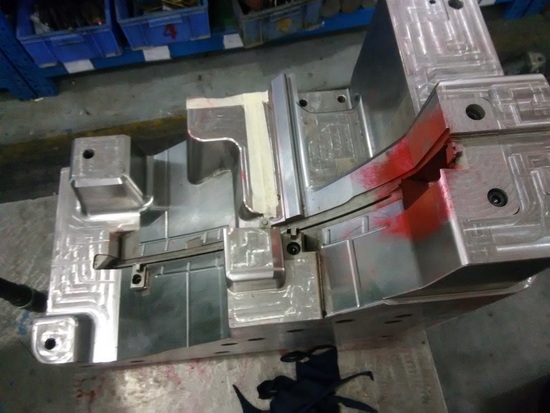
Lighting parts Cases : Audi Q5 SDI Mirro -Lens
Product material: transparent PMMA
Steel CAV / COR: H13 VAR (HRC55-60), the original material certificate is required, and the hardness of the front and rear molds is staggered. The product is highly polished, can’t pass the whetstone, save the mold to 1000# sandpaper and then polish. Glue surface/pattern surface: CNC makes the medium light and then discharges the mold. After the mold is finished flying, the high-speed machine is in place once, 20,000 rpm, and all the glue parts of the rear mold are assembled and fine-tuned together.
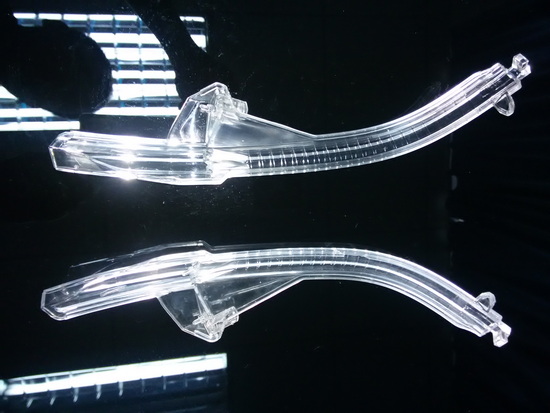
Lighting parts Cases : Audi Q5 SDI Mirro -Housing and bezel
Cavity and core steel : LG P-20 steel is used for the cavity HH P-20 and core molds (high polishing effect is required), and the original material certificate is provided, the front mold is HRC46-50, and the rear mold is HRC44-48.
The front mold (reflecting surface) is polished, and can not pass the whetstone, save the mold to 1000# sandpaper and then polish, the rear mold is generally 600#
CNC makes medium light and then discharges the mold. After flying the mold, the high-speed machine is in place at one time, 20,000 rpm, and all the glue position parts of the rear mold are assembled together, and then polished with a knife below 3MM.
BMC product steel can not be welded, heat treatment process and quality (can be hardened in the material factory) vacuum heat treatment
There should not be any sharp corners (including bottom holes) on the mold. The R angle should be as large as possible. Before hardening, deep-drill the heating pipe hole (plus 0.02), and then add the heating pipe and then harden it. Purchase the heating pipe itself needs to be minus 0.05 -0.1.
The exhaust is opened to the outside of the mold base, the exhaust is opened to the front mold, and the PL surfaces of the front and rear molds are effectively sealed to avoid air. The balance block needs to open the exhaust groove.
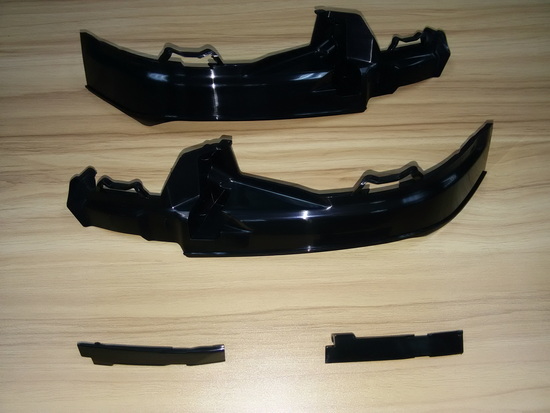